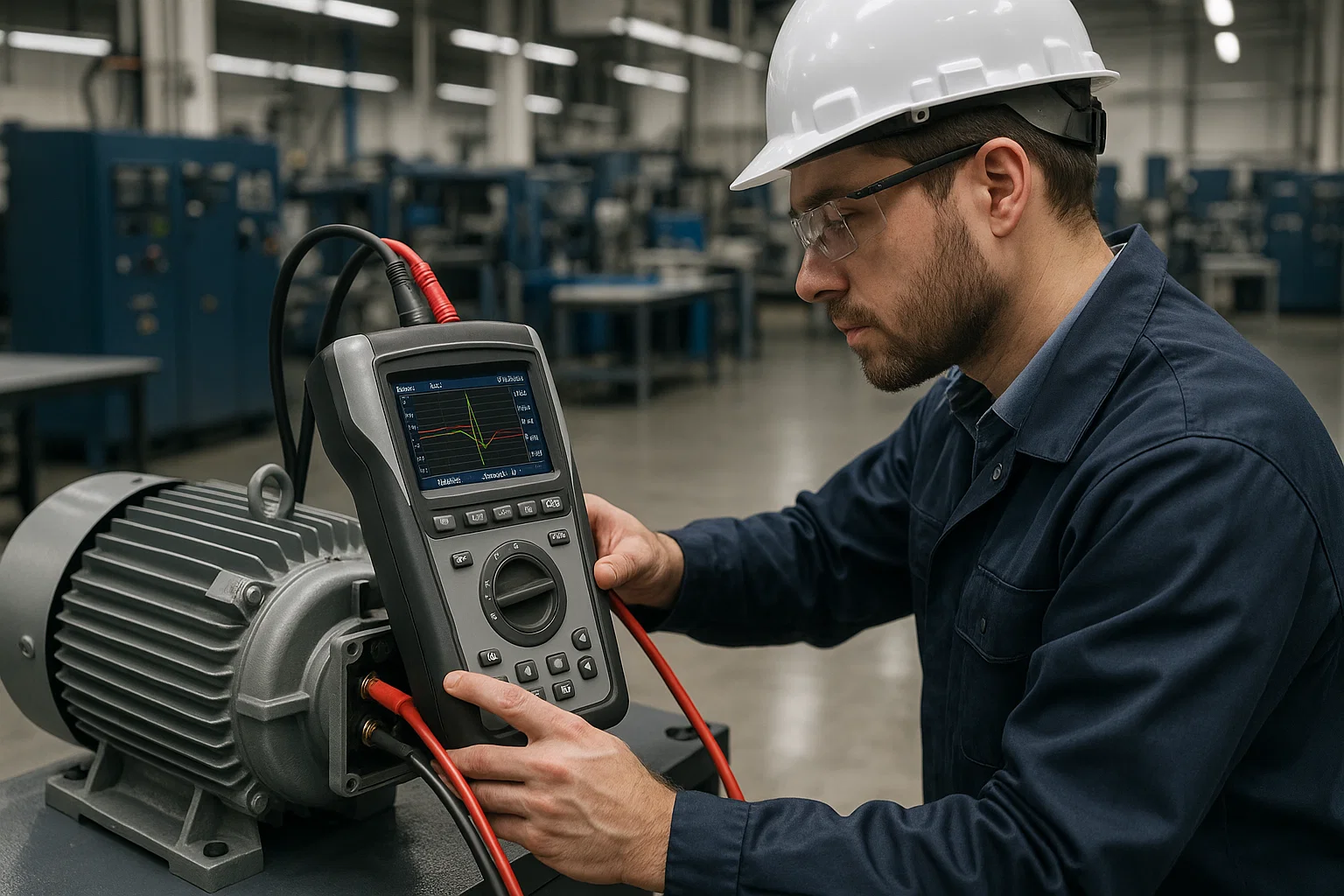
In the world of electrical maintenance and quality control, few tools are as critical yet as misunderstood as surge generators. When electrical systems fail unexpectedly, the costs can be astronomical—production downtime, emergency repairs, and potential safety hazards. What if you could identify winding insulation weaknesses before catastrophic failure occurs?
This is precisely where surge generators prove their worth. These specialized devices create controlled high-voltage pulses that help identify insulation weaknesses in motors, transformers, and other wound components before they lead to complete system failure.
At Vivid Metrawatt Global, we’ve seen firsthand how proper surge testing has saved our clients millions in potential downtime and replacement costs. In this comprehensive guide, we’ll explain exactly how surge generators work, their crucial role in immunity testing, and practical applications that can transform your maintenance strategy.
Surge generators (also known as surge testers or impulse winding testers) are specialized electrical test equipment designed to produce and apply high-voltage pulses to electrical systems. These controlled pulses mimic the electrical stress that motors and transformers experience during normal operation, but in a concentrated, measurable way.
At its core, a surge generator is a device that rapidly discharges stored electrical energy into a test specimen. This creates a high-voltage, short-duration pulse (or surge) that travels through the windings of motors, generators, or transformers.
The fundamental purpose of this process is to:
Unlike steady-state tests such as a megohmmeter test (which primarily tests ground insulation), surge testing specifically targets the turn and phase insulation that often fails first in electrical equipment.
To understand how surge generators work, we need to explore their fundamental operating principles:
The operation of a surge generator follows a simple yet precisely controlled cycle:
This cycle happens rapidly and can be repeated at various voltage levels to create a comprehensive test profile. For a more detailed breakdown of this process, see our guide on how to test motor windings.
When the capacitor discharges, it creates an oscillating waveform determined by the capacitance, inductance, and resistance of both the test circuit and the specimen being tested. This waveform is unique to each winding configuration—almost like a fingerprint of the motor or transformer’s internal structure.
The surge wave propagates through the winding, creating voltage differences between adjacent turns. If the insulation between these turns is weak, the surge will cause a partial breakdown, which appears as a change in the waveform pattern. Understanding these patterns is critical for troubleshooting common surge tester errors.
Modern digital surge testers consist of several critical components that work together to create controlled, precise test conditions:
The power supply converts standard line voltage to the higher voltage needed for testing. The charging circuit precisely controls the rate at which the capacitor charges, ensuring test repeatability.
This is where the electrical energy is stored before discharge. The capacitance value is carefully selected to match different testing requirements. Our high-power models like the 6kV Surge Tester High Power and 10kV-15kV Surge Tester High Power feature advanced capacitor banks for demanding applications.
Modern units use solid-state switches (thyristors or IGBTs) that provide precise timing control compared to older spark gap technology. These components are integral to how electromagnetic induction works in surge testing applications.
Advanced digital oscilloscopes capture the resulting waveforms with high resolution and sampling rates. Our LCD Surge Tester models feature integrated displays for immediate analysis.
Sophisticated algorithms compare waveforms, detect anomalies, and provide diagnostic information about the health of the winding insulation.
Multiple redundant safety features prevent accidental exposure to high voltage, including automatic discharge circuits, interlocks, and emergency stops. Safety is a critical consideration in all our designs, from basic models to our advanced 50kV Digital Surge Tester.
Surge generators play a fundamental role in immunity testing—a critical aspect of both manufacturing quality control and ongoing maintenance programs.
Immunity testing assesses how well an electrical system can withstand transient overvoltages without experiencing damage or malfunction. These transients occur in real-world operations due to:
Surge protection devices are designed to guard against these very events, and surge generators help verify their effectiveness.
Several international standards mandate surge testing for different applications:
Compliance with these standards often requires documented surge testing at specified voltage levels, which can only be properly performed with calibrated surge generators. These standards frequently require high voltage testing as part of the certification process.
Surge generators serve two distinct testing purposes:
Preventive Maintenance Testing: Performed periodically on installed equipment to track insulation deterioration over time. The test results are compared with baseline measurements to identify degradation before failure occurs.
Acceptance Testing: Conducted on new or repaired equipment to verify manufacturing quality and ensure the equipment meets specified standards before installation.
The applications of surge generators extend across numerous industries and scenarios. Here are some of the most common practical use cases:
Manufacturers use surge testing as a final quality check to ensure their motors meet design specifications. This identifies manufacturing defects like:
The benefits of using surge testers in manufacturing include significant reduction in warranty claims and enhanced product reliability.
After repair or rewinding, surge testing provides verification that the work was properly performed. This is particularly important for critical equipment where failure would result in significant downtime. Techniques for testing armature using a surge tester are especially valuable in motor repair shops.
Regular surge testing as part of a scheduled maintenance program allows for trending of insulation condition over time. This predictive approach enables:
For single-phase motors, specialized techniques help test windings efficiently.
When motors experience mysterious trips or performance issues, surge testing can identify weak insulation that might only fail under certain operating conditions. Learning to recognize motor winding failure signs can help maintenance teams address problems before catastrophic failure.
After lightning strikes, power surges, or other electrical events, surge testing helps determine if equipment has sustained hidden damage that might lead to future failure. For three-phase motors, specialized testing procedures can identify damage that might not be apparent through other test methods.
Motors exposed to moisture, chemicals, or extreme temperatures may experience insulation degradation that isn’t visible but can be detected through surge testing. Understanding common surge tester insulation failures helps interpret test results correctly in these scenarios.
The evolution from analog to digital surge testing technology has dramatically improved test capabilities and result interpretation.
Traditional analog surge testers display waveforms on an oscilloscope screen, requiring technicians to visually compare patterns. While effective in skilled hands, this approach has limitations:
These limitations become especially apparent when comparing surge testers vs. hipot testers, as modern digital technology offers significant advantages in both applications.
Modern digital surge testers offer significant advantages:
The digital approach eliminates subjectivity and provides quantifiable results that can be tracked over time, making it easier to detect gradual insulation deterioration. This technology has revolutionized how surge testing enhances motor reliability and efficiency.
Selecting the appropriate surge generator requires careful consideration of several factors:
The surge generator must provide sufficient voltage for the equipment being tested. Generally:
For specialized applications, such as armature testing, dedicated models like our 1kV Digital Armature Surge Tester provide optimized performance.
Modern units often combine multiple test functions:
Our guide on choosing the right surge tester for your needs provides additional insights into this selection process.
Consider where testing will occur:
Evaluate how test results will be handled:
The complexity of operation affects training requirements and test reliability:
To ensure accurate and reliable surge testing, proper maintenance and calibration of surge generators is essential.
Most manufacturers recommend annual calibration, but critical applications may require more frequent verification. Calibration should include:
Regular maintenance tasks include:
For detailed guidance on maintaining your specific model, refer to our guide on how to maintain and calibrate your digital surge tester.
The field of surge testing continues to evolve with several emerging trends:
AI algorithms are being developed to automatically identify patterns in surge test results that might indicate specific types of insulation problems, even before they become severe enough to cause standard test failures. These advancements are expanding the applications of digital surge testers beyond traditional uses.
Connected surge testers can automatically upload test results to centralized databases, enabling fleet-wide analysis and more sophisticated predictive maintenance programs. This connectivity is transforming how maintenance teams approach motor reliability across multiple facilities.
New approaches allow for higher voltage testing without risking damage to good insulation, providing better discrimination between healthy and problematic windings. This is especially valuable for critical equipment where downtime must be minimized.
The trend toward comprehensive test platforms that combine surge testing with other electrical and mechanical tests (vibration, current analysis, etc.) provides a more complete picture of motor health.
Advances in power electronics are enabling smaller, more portable surge testers with capabilities previously only available in larger units.
Surge generators represent a critical technology in the electrical testing arsenal. By understanding how they work and applying them properly, maintenance professionals can:
The evolution from simple analog devices to sophisticated digital systems has dramatically improved test capabilities and result interpretation. As the technology continues to advance, we can expect even more powerful diagnostic capabilities that will further enhance equipment reliability and reduce maintenance costs.
At Vivid Metrawatt Global, we’re committed to providing the most advanced surge testing technology and the knowledge needed to apply it effectively. Whether you’re looking to establish a new testing program or upgrade your existing equipment, our team is ready to help you implement solutions that protect your critical assets.
For more information about specific surge tester models or to discuss your unique testing requirements, visit our digital surge tester product page or contact our expert team. We provide customer support for all our products and can help you determine the right solution for your specific application.