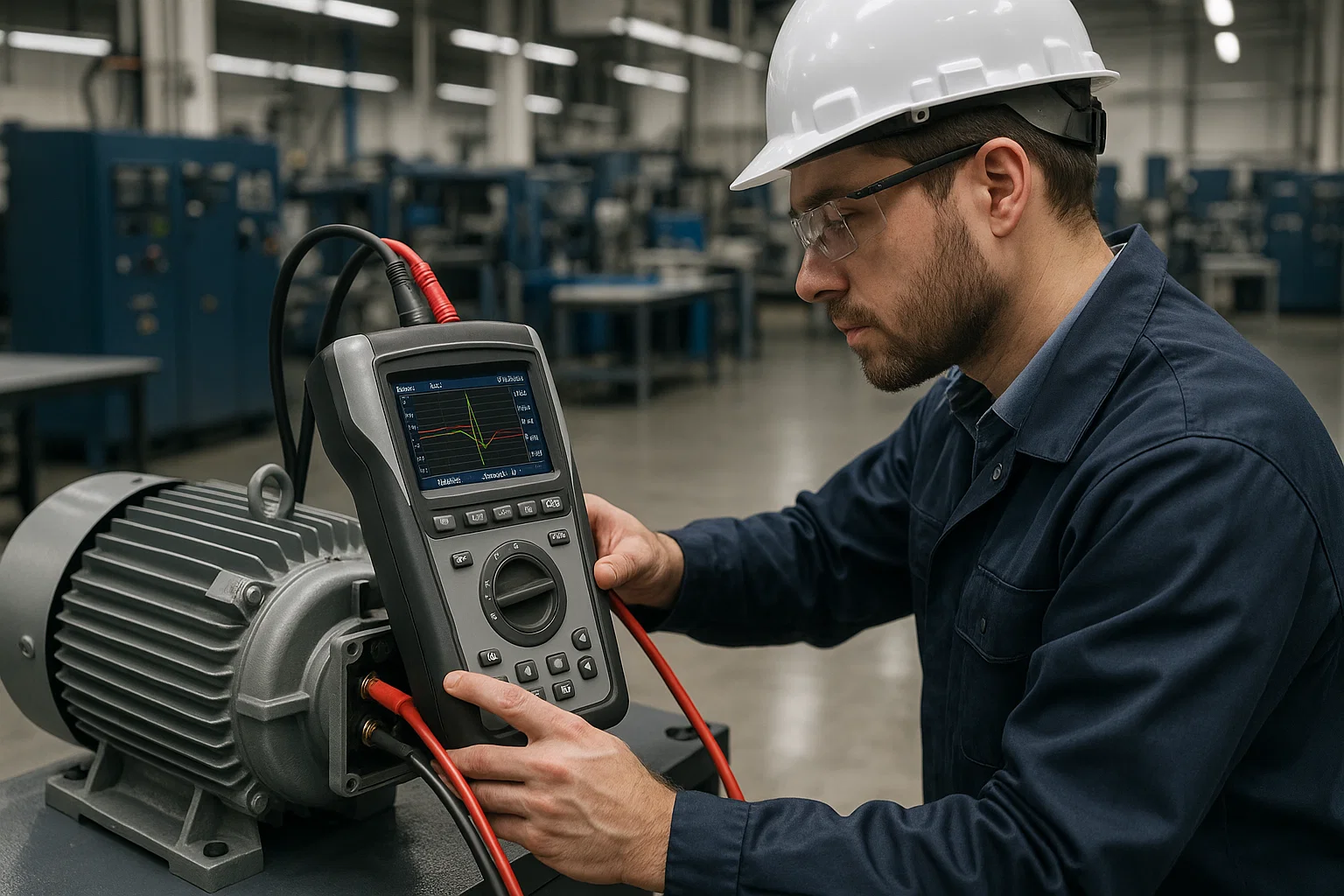
Selecting the right material for induction hardening can be the difference between component success and failure. When inappropriate materials are used, manufacturers face wasted resources, compromised part integrity, and potentially catastrophic equipment failures. This comprehensive guide explores the common materials used in induction hardening processes, helping you make informed decisions for your specific applications and achieve superior hardness with optimal efficiency.
Induction hardening is a specialized heat treatment process that uses electromagnetic induction to heat ferromagnetic materials rapidly. This process creates a hardened layer (case) on the surface while maintaining the component’s tough, ductile core. The technology relies on inducing electrical currents within the workpiece, generating localized heat without direct contact.
At Vivid Metrawatt Global, induction hardening is recognized as one of the most efficient surface hardening methods, offering precision, speed, and environmental advantages over traditional heat treatment approaches.
The success of induction hardening depends significantly on material selection. Here are the most commonly used materials in this process:
Medium-Carbon Steels (0.35% to 0.55% Carbon)
Medium-carbon steels represent the most widely used materials for induction hardening applications. These steels strike an ideal balance between hardenability and core toughness.
Common examples include:
Their popularity stems from excellent response to induction heating, predictable hardening behavior, and cost-effectiveness. Components like gears, shafts, and sprockets frequently utilize these materials.
High-Carbon Steels (0.60% to 1.00% Carbon)
High-carbon steels provide exceptional surface hardness after induction treatment:
These materials are ideal for applications requiring extreme wear resistance, though they may be more susceptible to cracking if process parameters aren’t carefully controlled.
Chromium-Molybdenum Steels
Chromium-molybdenum steels offer superior hardenability compared to plain carbon steels, making them excellent candidates for induction hardening:
These alloys achieve deeper hardening with less risk of distortion, which is particularly valuable for larger components or those with complex geometries.
Nickel-Chromium Steels
Nickel-chromium alloys deliver exceptional toughness alongside good hardenability:
These materials are frequently selected for components requiring both surface hardness and excellent core properties, such as heavy-duty gears and critical automotive parts.
Tool steels represent premium materials for induction hardening, offering exceptional wear resistance and dimensional stability:
Water-Hardening Tool Steels
Oil-Hardening Tool Steels
Air-Hardening Tool Steels
Tool steels are typically used for cutting tools, dies, and high-wear components where operational demands justify their higher cost.
Certain cast iron grades respond well to induction hardening:
Ductile (Nodular) Cast Iron
Gray Cast Iron (select grades with appropriate carbon content)
Cast irons require careful process control during induction hardening to prevent cracking, but when properly processed, they can achieve excellent surface hardness.
For specialized applications, several other materials can undergo induction hardening:
Powder Metallurgy Components PM components with appropriate carbon content and density can be successfully induction hardened, though porosity must be carefully managed.
Precipitation Hardening Steels
These materials combine the benefits of stainless steels with hardenability, offering corrosion resistance alongside improved surface properties.
Learn more about specialty material processing in our Advanced Materials Processing Guide.
Selecting the optimal material for induction hardening requires consideration of several key factors:
Carbon content is the single most critical factor in determining a material’s suitability for induction hardening. Generally:
Different alloying elements influence hardenability and resultant properties:
The starting condition significantly affects induction hardening results:
Geometry directly influences material selection:
Our Engineering Solutions team can assist with material selection based on your specific component geometry and performance requirements.
Understanding how different materials perform during induction hardening helps make informed selections:
Low Distortion Materials:
Higher Distortion Risk:
When evaluating materials, consider both material and processing costs:
Cost-Effective Options:
Premium Materials (Higher Cost):
Different industries leverage specific materials for induction hardening based on performance requirements:
Crankshafts and Camshafts:
Transmission Components:
Steering and Suspension:
Heavy Equipment Components:
Power Transmission:
Hydraulic Components:
Punches and Dies:
Cutting Edges:
Proper material preparation is essential for successful induction hardening:
Even with proper material selection, challenges can arise during induction hardening:
Soft Spots:
Cracking:
Inconsistent Case Depth:
Carbon Steels:
Alloy Steels:
Tool Steels:
Cast Irons:
Induction hardening commonly uses medium-carbon steels (0.35-0.55% carbon), alloy steels containing chromium, molybdenum, and nickel, tool steels, and certain grades of cast iron. The carbon content is critical, as materials with less than 0.30% carbon generally don’t respond well to this process.
1045 steel (0.45% carbon) is generally considered optimal for most induction hardening applications, offering an excellent balance of hardenability, core toughness, and cost-effectiveness. For higher hardness requirements, 1060 or 1070 steels may be preferred.
Most austenitic stainless steels (300 series) cannot be effectively induction hardened. However, martensitic stainless steels like 410, 420, and 440C can be successfully hardened using induction processes, as can precipitation hardening grades like 17-4 PH.
Carbon content directly determines a material’s hardenability and maximum achievable hardness. Materials need sufficient carbon (typically minimum 0.35%) to form martensite during quenching, which provides the desired hardness. Higher carbon contents generally yield higher hardness but may increase cracking risks.
The most critical factors are carbon content (minimum 0.35% for effective hardening), hardenability (influenced by alloying elements), section thickness (affects power requirements and case depth), prior condition (normalized is preferred), and end-use requirements (wear resistance, fatigue strength).
Alloy steels contain elements like chromium, nickel, and molybdenum that enhance hardenability, allowing deeper case depths and more uniform hardening, particularly in thicker sections. They typically exhibit less distortion and better properties throughout the hardened zone compared to carbon steels.
Yes, certain grades of cast iron, particularly ductile (nodular) iron with appropriate matrix structures, can be successfully induction hardened. However, they require careful process control to prevent cracking, and the graphite structure impacts the magnetic field and resulting hardening pattern.
Carbon steels offer cost-effectiveness and good hardness but limited hardenability. Alloy steels provide superior hardenability and properties but at higher cost. Tool steels deliver exceptional wear resistance but with increased cracking risk and cost. Cast irons can be hardened selectively but require precise control and have limited case depth potential.
Materials should ideally be normalized to ensure consistent microstructure, thoroughly cleaned to remove contaminants, checked for decarburization (which inhibits hardening), and sometimes stress-relieved if previously worked. Surface condition should be consistent to ensure uniform heating.
Material composition directly impacts magnetic permeability and electrical resistivity, which determine induction heating effectiveness. Higher carbon and silicon content generally improve magnetic properties. Alloying elements affect the coupling efficiency and power requirements, with highly alloyed steels often requiring more energy to achieve the same temperature.
Selecting the appropriate material for induction hardening is fundamental to achieving desired mechanical properties and component performance. Medium-carbon steels remain the most widely used option for their excellent balance of properties and cost-effectiveness, while alloy steels offer enhanced performance for more demanding applications.
By understanding the relationship between material composition, hardenability, and process parameters, manufacturers can optimize their induction hardening operations for maximum efficiency and quality. The right material choice, combined with proper preparation and process control, ensures consistent, high-quality results across diverse industrial applications.
For personalized assistance with material selection and induction hardening process optimization, contact the experts at Vivid Metrawatt Global today.