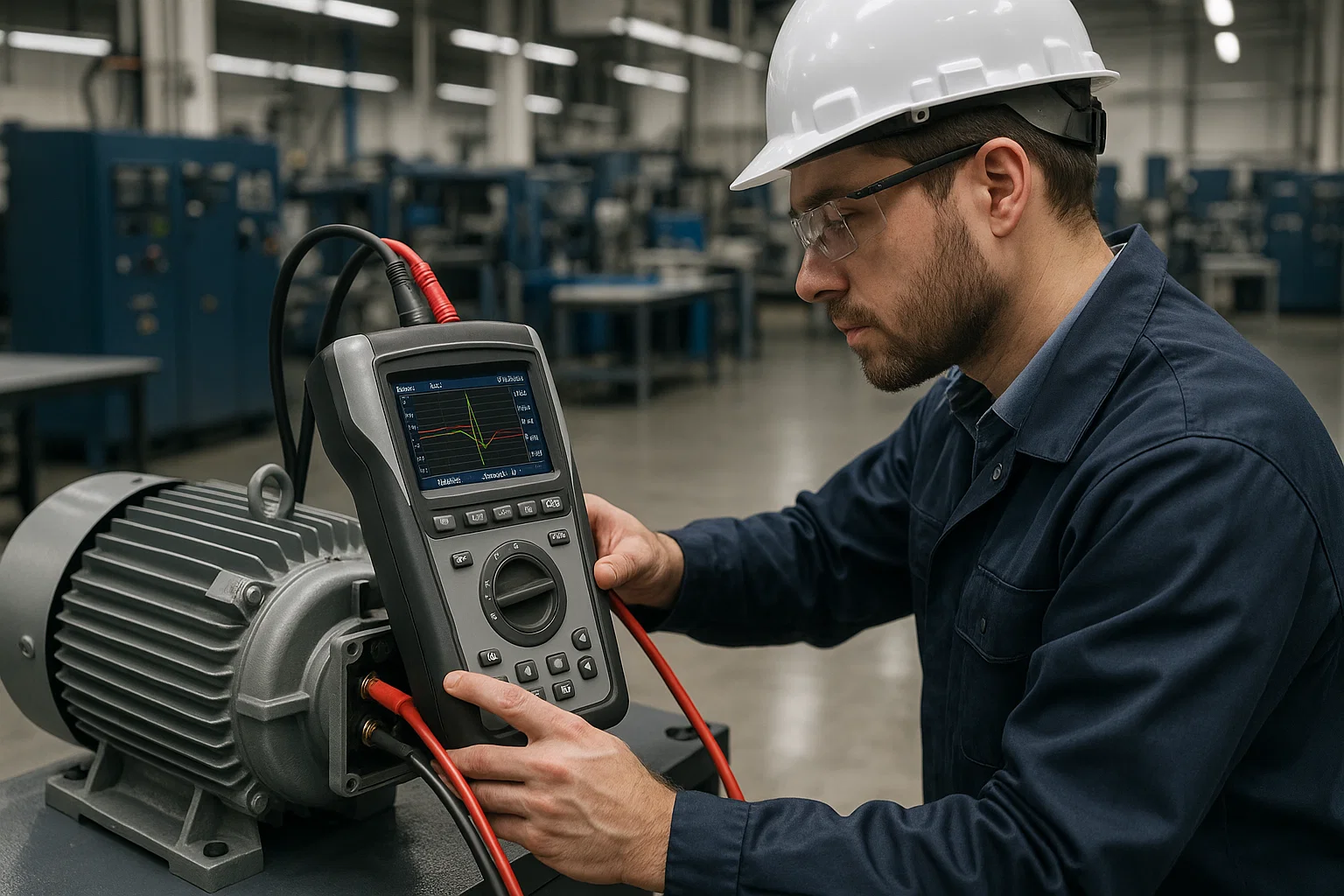
Single-phase motors play an essential role in many of our everyday devices, whether it’s powering a fan, a washing machine, or industrial equipment. Over time, these motors can experience wear and tear, and when they fail, the windings are often the culprit. But how to test windings on a single phase motor to diagnose the problem? Let’s walk through this together in a way that anyone can understand, without overwhelming jargon.
The heart of a single-phase motor lies in its windings. These are copper wires coiled in such a way that they create a magnetic field when electricity passes through them. This magnetic field is what drives the motor to rotate, powering the machines we rely on daily. If something goes wrong with the windings, the motor can struggle or stop working altogether.
Before diving into testing, it’s important to recognize the signs that your motor’s windings may need attention:
When any of these symptoms arise, it’s time to test the windings to determine if they’re causing the issue.
To properly test the windings, you’ll need some basic tools:
Having these tools at hand will make the testing process easier and safer.
Before you start, always ensure that the motor is disconnected from the power source. Testing a live motor can be dangerous, so double-check that the motor is completely isolated from any electrical supply.
– The resistance value should be low but not zero. If it’s zero, this suggests a short circuit.
– A high resistance reading may indicate the winding is partially burnt or damaged.
– If the meter shows a very low reading or zero, the winding is shorting to the ground, meaning the motor needs to be repaired or replaced.
After completing the tests, you’ll have a clearer idea of the state of your motor windings:
Testing the windings helps you determine whether the motor can be repaired or if replacement is the better option. If the motor is old and has multiple issues like ground faults and high resistance, replacing it might be more cost-effective. But if the problem is isolated to a single winding and the rest of the motor is in good condition, rewinding or repairing the motor could extend its lifespan.
Taking the time to test the windings on a single-phase motor ensures you catch problems early. It might seem like a technical task, but once you have the right tools and follow the steps, it becomes much more manageable. Testing can save you from bigger failures down the road, whether you’re maintaining equipment in your workshop or troubleshooting a household appliance. Keep your motors running smoothly and avoid costly replacements by learning to test and care for the windings yourself.