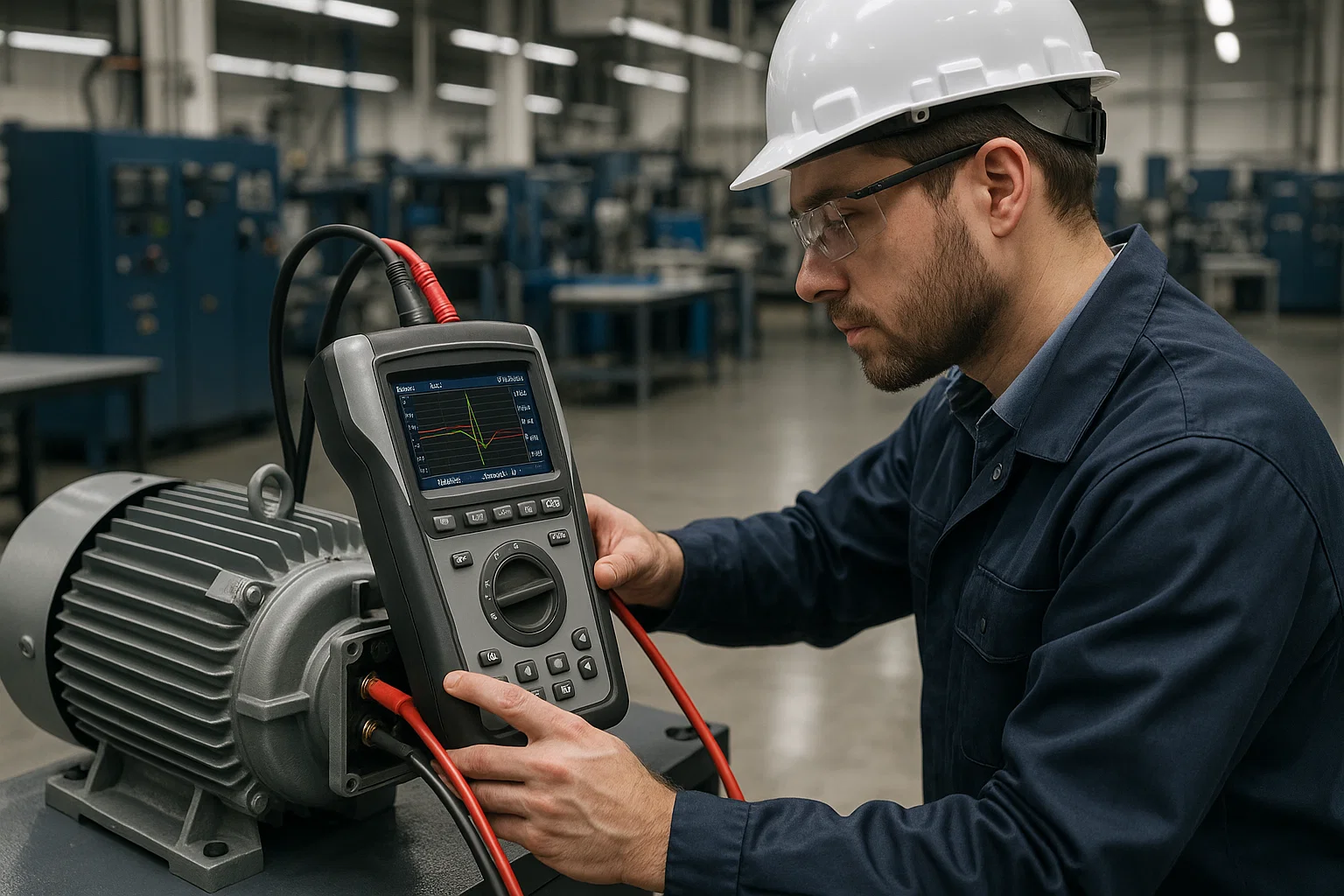
Designing an effective induction heating coil is often the difference between operational excellence and costly inefficiencies. Despite its critical importance in manufacturing processes, many engineers struggle with optimizing coil configurations that deliver precise, uniform heating while minimizing energy consumption. Without proper design considerations, businesses face increased power costs, inconsistent product quality, and reduced equipment lifespan. This comprehensive guide provides advanced, actionable insights into induction heating coil design that will transform your thermal processing operations and deliver measurable improvements in both efficiency and precision.
Induction heating operates on the principle of electromagnetic induction, where alternating current passing through a coil generates a magnetic field that induces eddy currents in conductive materials. These currents produce heat through Joule heating and magnetic hysteresis. The effectiveness of this process directly correlates with how well your coil design matches the workpiece characteristics and desired heating pattern.
At its core, successful induction heating depends on:
When designing induction heating systems, it’s crucial to understand that the coil serves as both the heating element and the applicator, making its design particularly critical to the entire process efficiency.
The operating frequency significantly influences heating patterns and efficiency:
Selecting the appropriate frequency range is the foundation of your coil design process and will determine many subsequent design decisions.
Coil geometry dramatically impacts heating uniformity and energy transfer. Consider these critical design aspects:
Achieving precise heating patterns requires careful attention to power density distribution:
Balancing power density requirements with practical constraints is essential for optimal coil performance. Each application presents unique challenges that demand thoughtful engineering approaches.
Beyond basic helical coils, advanced applications often require sophisticated configurations:
These specialized designs solve challenging heating requirements where standard configurations would fail.
For complex processes, multiple coils working in coordination offer superior results:
Synchronizing multiple coils requires sophisticated power control systems and timing coordination. The benefits include more uniform temperature profiles, reduced cycle times, and improved energy efficiency.
The coil conductor material significantly impacts performance and durability:
Material selection must balance electrical performance with mechanical strength and thermal stability.
Effective cooling is essential for coil longevity and consistent performance:
The cooling system design must consider both thermal transfer and hydraulic flow characteristics to prevent hotspots while minimizing pressure drop.
Modern coil design relies heavily on computational methods:
These tools enable engineers to visualize field patterns, predict heating profiles, and optimize designs before physical prototyping.
Creating high-performance coils requires exacting fabrication techniques:
Manufacturing precision directly impacts coil performance, especially for high-frequency applications where small geometric variations significantly affect field distribution.
Effective cooling is critical for preventing coil overheating and ensuring consistent performance:
Inadequate cooling is the leading cause of coil failure in high-power applications.
Integrating sensors and protection mechanisms safeguards your investment:
These monitoring systems should be integrated into the overall control architecture to provide both protection and performance data.
Maximizing electrical efficiency requires proper matching between power supply and coil:
A properly matched system can improve efficiency by 15-30% compared to unoptimized configurations. For comprehensive power system solutions, contact our efficiency experts.
Strategic use of magnetic materials enhances performance:
These components can dramatically improve coupling efficiency while providing precise control over heating patterns.
Modern design processes use simulation to reduce development time:
Virtual testing identifies potential issues before fabrication, reducing iterations and accelerating development. Our engineering team utilizes advanced simulation techniques to ensure first-time-right designs.
Comprehensive testing confirms simulated predictions:
These validation methods provide confidence in design performance and establish baseline metrics for process control.
When coils don’t perform as expected, systematic troubleshooting is essential:
Identifying root causes requires understanding the interrelationships between electrical, thermal, and mechanical factors.
Preventive strategies extend coil life and maintain performance:
Proper maintenance significantly extends operational life while maintaining consistent performance characteristics.
The field continues to evolve with innovative approaches:
Staying current with technological advances ensures your heating systems remain competitive.
Modern induction systems increasingly incorporate smart manufacturing capabilities:
These capabilities transform traditional heating operations into data-driven, continuously improving processes.
The number of turns directly impacts inductance and field distribution. More turns increase total inductance and provide more uniform heating across larger areas, while fewer turns deliver more intense, localized heating. The optimal number depends on your specific application, workpiece size, and power supply characteristics.
While there’s no universal “ideal” distance, most applications perform best with a gap of 0.5-3mm between the coil and workpiece. Tighter coupling increases efficiency but may cause arcing or uneven heating, while larger gaps reduce efficiency but may provide more uniform temperature distribution for certain geometries.
Water provides superior cooling efficiency and is preferred for most applications. However, oil cooling may be necessary when electrical isolation is critical or when operating in environments where water leakage could cause safety hazards. The decision involves balancing thermal performance against dielectric strength requirements.
High-conductivity copper remains the standard for most applications due to its excellent electrical and thermal properties. For specialized applications, silver-plated copper, beryllium copper alloys, or even aluminum may be preferred based on specific requirements for strength, temperature resistance, or weight.
Proper cooling design is essential, including adequate water flow, appropriate tube diameter, and strategic placement of cooling channels. Additionally, monitoring systems, thermal insulation between coil and workpiece, and proper power settings all contribute to preventing overheating issues.
Solenoid (helical) coils create a concentrated field inside the coil, making them ideal for heating rod-shaped or cylindrical workpieces. Pancake coils produce a field perpendicular to the coil plane, making them suitable for surface heating of flat workpieces or for applications requiring one-sided access.
Higher frequencies require coils with greater attention to geometric precision and typically use smaller diameter tubing with tighter spacing. Lower frequencies allow more design flexibility but generally demand higher current-carrying capacity. The coil must be designed specifically for the frequency range of your power supply.
Flux concentrators direct magnetic energy to specific areas, increasing efficiency by up to 30% while reducing stray fields. They enable more precise heating patterns, allow lower power settings, and can protect sensitive components from unintended heating effects.
Complex geometries often require conforming coils that match the workpiece shape. Design approaches include segmented coils, variable pitch winding, multiple independent coils, or custom-shaped single coils. Simulation software is invaluable for optimizing these configurations before fabrication.
Regular maintenance should include inspection for discoloration or deformation, cleaning of cooling passages, checking electrical connections and insulation, and verification of cooling system flow rates. Preventive maintenance schedules depend on operating conditions, but quarterly inspections are typical for high-duty applications.
Designing optimal induction heating coils requires balancing multiple interdependent factors including geometry, materials, cooling, and electrical characteristics. By applying the advanced principles outlined in this guide, engineers can achieve significant improvements in heating efficiency, temperature precision, and process reliability.
The most successful designs emerge from systematic approaches that combine theoretical understanding with practical experience and leverage both computational modeling and experimental validation. For complex applications, partnering with specialists can accelerate development and ensure optimal results.
Contact our engineering team to discuss your specific induction heating challenges and discover how our expertise can help optimize your thermal processing operations.