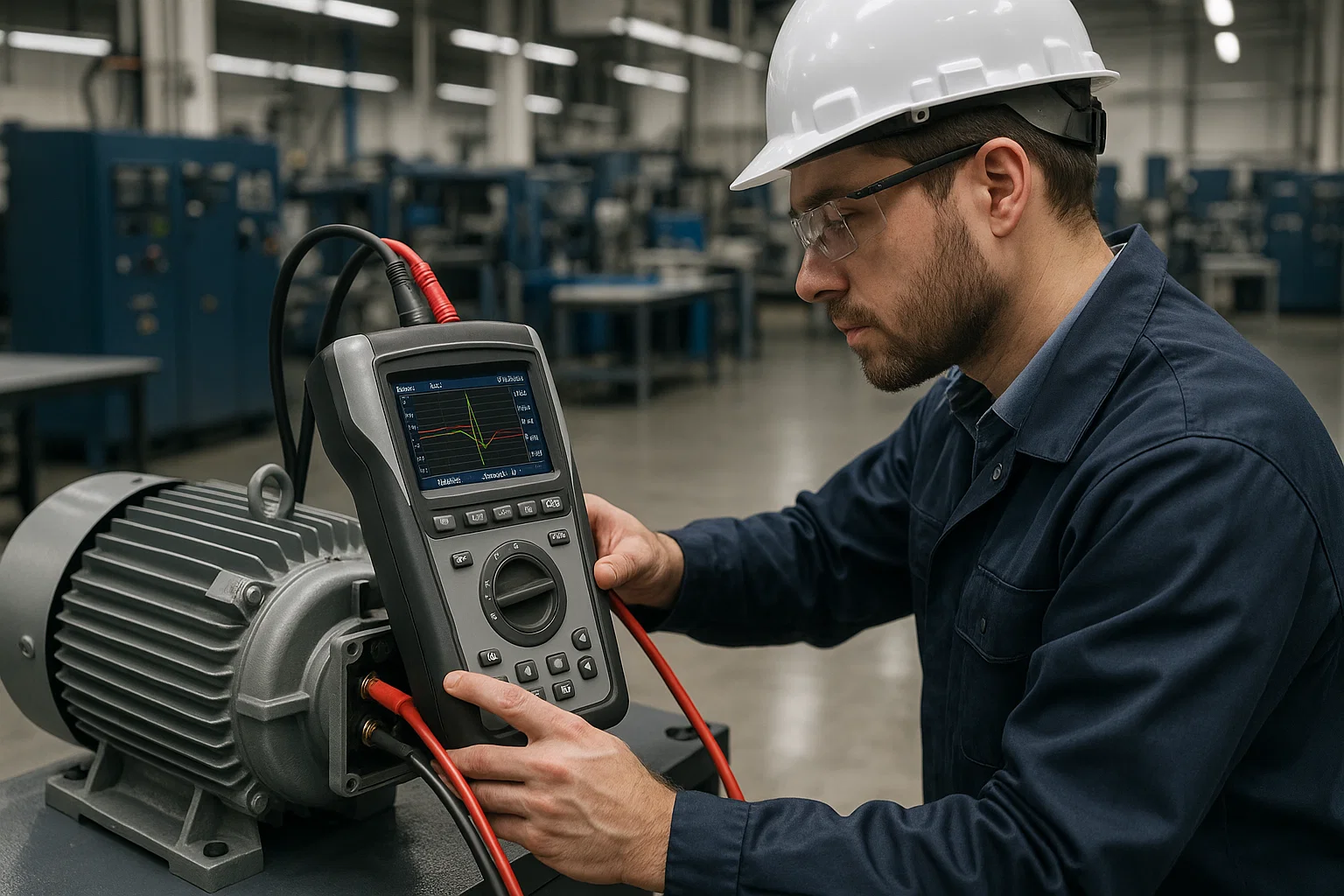
The automotive industry has always been at the forefront of adopting innovative technologies to improve production efficiency, precision, and overall product quality. One such technological advancement is the use of induction heaters. These devices are revolutionizing the way automotive components are manufactured, assembled, and repaired, offering multiple benefits that enhance performance, reduce energy consumption, and increase safety.
In this blog, we will explore the key benefits of induction heaters for the automotive industry, explaining how these systems work and why they are becoming a popular choice for various automotive applications.
Induction heating is a process used to heat electrically conductive materials using electromagnetic induction. It involves passing an alternating current through a coil, creating a magnetic field that induces an electric current in the material being heated. This current generates heat within the material itself, allowing for fast and efficient heating.
Unlike traditional heating methods such as furnaces or open flames, induction heating offers precise control over the heating process, enabling uniform temperature distribution without the need for direct contact between the heat source and the material. This makes it particularly useful in industries that require high levels of precision and efficiency, like the automotive sector.
Induction heaters used in the automotive industry typically consist of a coil, a power supply, and a workpiece. When a workpiece, such as a metal part of a car engine or transmission, is placed within the coil, an alternating current flows through the coil, generating a high-frequency magnetic field. This magnetic field induces an electric current in the workpiece, which in turn generates heat.
The heating process can be carefully controlled, allowing manufacturers to heat parts to the exact temperature required for a specific operation, such as hardening, brazing, or pre-heating before assembly. The ability to heat parts selectively without affecting the surrounding areas ensures minimal thermal distortion, contributing to the overall quality and performance of the final product.
Induction heating allows for extremely precise temperature control. In the automotive industry, where even small temperature deviations can affect the performance and quality of components, this precision is crucial. Induction heaters provide fast and localized heating, which means that manufacturers can heat specific areas of a component without affecting its entire structure. This is particularly beneficial for processes like surface hardening and shrink fitting, where accuracy is paramount.
Induction heating is more energy-efficient than traditional heating methods. Traditional heating methods, such as furnaces or ovens, often waste a significant amount of energy in the form of heat loss to the surrounding environment. In contrast, induction heating directly heats the workpiece, making it more energy-efficient. This reduction in energy consumption translates to lower operating costs for automotive manufacturers and a smaller carbon footprint, aligning with the industry’s growing focus on sustainability.
Induction heaters provide faster heating times compared to conventional methods. The rapid heating process not only speeds up the overall production cycle but also minimizes downtime between operations. For automotive manufacturers aiming to increase throughput and reduce lead times, induction heating can be a game-changer. Parts can be heated in a matter of seconds, allowing for quicker assembly and testing, ultimately reducing production costs and improving operational efficiency.
Induction heating helps maintain the integrity of automotive components. Because the heating process is so localized and precise, there is less risk of distorting or damaging parts during manufacturing. Induction heating can also be used to improve the hardness and durability of components through processes like induction hardening, which involves heating a metal part and then quickly cooling it to increase its strength. This is especially important in automotive applications, where parts are subjected to high stress and must meet rigorous durability standards.
Induction heating offers significant safety and environmental benefits. Unlike traditional heating methods that involve open flames or high temperatures, induction heating is a clean and controlled process. This reduces the risk of workplace accidents related to fires, burns, and heat stress. Additionally, since induction heating uses less energy and produces fewer emissions, it contributes to a more sustainable manufacturing process.
Induction heating plays a critical role in various automotive manufacturing processes. Here are some of the most common applications:
Hardening and Tempering: Induction heating is widely used for hardening and tempering metal components, such as gears, shafts, and crankshafts. The process ensures that these parts are tough, durable, and capable of withstanding heavy use and high pressures.
Brazing and Soldering: Induction heaters are also used in brazing and soldering processes to join metal parts without compromising their structural integrity. These processes are common in the assembly of complex automotive systems like radiators and exhaust systems.
Shrink Fitting: Induction heating is used in shrink fitting, where components are heated to expand before being fitted together. This process is critical for fitting bearings, bushings, and other parts into precise locations without damaging the surrounding structures.
Preheating Before Welding: Induction heaters can be used to preheat materials before welding, ensuring that the metals are at the correct temperature for optimal weld quality and minimizing the risk of cracking or warping during the welding process.
Surface Hardening: Induction hardening is used to increase the surface hardness of automotive components, providing greater resistance to wear and tear while maintaining a tough core for strength.
The benefits of induction heating in the automotive industry are undeniable. From improving precision and energy efficiency to speeding up production and enhancing component integrity, induction heaters are transforming how automotive parts are manufactured. As the automotive sector continues to evolve and demand higher quality, more sustainable practices, induction heating offers an effective solution to meet these challenges.
By adopting induction heating technology, automotive manufacturers can achieve better product performance, reduced costs, and a more sustainable manufacturing process. As a result, induction heaters are poised to play a crucial role in shaping the future of automotive production.
If you’re looking to enhance your automotive manufacturing processes, adopting induction heating technology is a step in the right direction.